Finding the Perfect Fit for Your Needs
Wire harnesses are essential components in countless industries, from automotive and aerospace to telecommunications and medical devices. Consequently, understanding wire harness manufacturing and choosing the right wire harness assembly partner can make all the difference in the quality, reliability, and cost-effectiveness of your final product. Therefore, this article outlines key factors to consider when making this critical decision.
1. Wire Harness Manufacturing: Expertise and Experience
- When seeking an assembly partner, first and foremost, prioritize their industry knowledge, especially in wire harness manufacturing. Specifically, look for a partner with a proven track record in your industry, as they should understand the unique challenges and requirements of your applications.
- In addition to industry expertise, consider their technical skills. Ensure that the partner possesses the necessary technical expertise in wire harness manufacturing and has a team of skilled technicians capable of handling your project’s complexity.
- Finally, confirm that they adhere to relevant quality standards. For example, check if they comply with standards like IPC/WHMA-A-620 when it comes to wire harness manufacturing and hold appropriate certifications, such as UL or CSA.
2. Wire Harness Manufacturing: Manufacturing Capabilities
Firstly, it’s essential to determine if the potential partner has the capacity to handle both your current and future production needs. To do this, thoroughly assess their production capacity and scalability in it. Secondly, inquire about their equipment. Do they utilize the latest technology and equipment to ensure efficient and precise assembly? Lastly, flexibility is key. It’s important to ascertain whether they can adapt to your changing needs and accommodate design revisions or custom requests.
3. Wire Harness Manufacturing: Quality and Reliability
- Quality Control: Inquire about their quality control processes. Do they have rigorous inspection and testing procedures in place?
- Materials: Do they use high-quality materials from reputable suppliers in their wire harness manufacturing process?
- Traceability: Can they provide traceability documentation for all components and processes involved in it?\
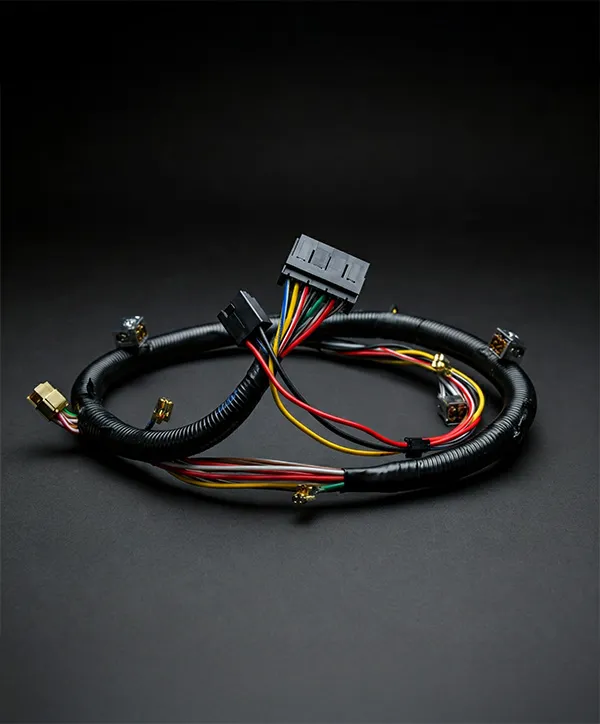
4. Wire Harness Manufacturing: Communication and Collaboration
- Responsiveness: Are they responsive to your inquiries and concerns?
- Collaboration: Do they foster a collaborative environment and actively involve you in the manufacturing process?
- Problem-solving: Are they proactive in identifying and addressing potential issues?
5. Cost and Delivery
- Competitive Pricing: Obtain quotes from multiple assembly partners to ensure competitive pricing.
- Value: Consider the overall value proposition, balancing cost with quality, reliability, and service.
- Delivery: Can they meet your delivery deadlines consistently?
6. Customer References and Reputation
- References: Ask for customer references and testimonials related to their services.
- Reputation: Research their reputation in the industry and look for online reviews or case studies.
7. Location and Logistics
- Proximity: Consider their location and its impact on logistics, transportation costs, and lead times.
- On-site Visits: If possible, visit their facility to assess their operations and capabilities firsthand.
Conclusion
Selecting the right assembly partner is undeniably a crucial decision that can significantly impact your business’s success. Therefore, by carefully evaluating potential partners based on these key factors, you can ultimately find the perfect fit for your specific needs. Furthermore, this meticulous selection process will ensure a long-lasting, mutually beneficial relationship.